Unused product labels can face various issues over time if not stored correctly. This article looks into the shelf life of unused labels, factors affecting their durability, and best practices for storage to ensure they remain effective.
Do Unused Product Labels Have a Shelf Life? Understanding Durability and Storage
The Importance of Knowing Label Shelf Life
Cost Considerations and Bulk Ordering
Ordering labels in bulk can seem like a great way to save money. The unit price typically decreases as the quantity increases, making large orders appear cost-effective. However, there are hidden costs to consider.
- Storage Costs: Storing large quantities of labels may require additional space and handling, increasing your overall costs.
- Obsolescence Risk: Labels can become outdated due to regulatory changes or product updates, leading to wasted inventory and the need for reprints.
Potential Issues with Excess Inventory
Having a large inventory of labels can lead to several potential issues beyond just storage.
- Label Deterioration: Over time, labels can lose their adhesive strength and overall quality if not stored properly.
- Regulatory Changes: Changes in labeling laws can render your labels obsolete, requiring expensive reprints and redesigns.
- Product Updates: If your product formula or branding changes, old labels can no longer be used, leading to waste.
Factors Affecting the Shelf Life of Product Labels
Adhesive Deterioration Over Time
The adhesive on labels is crucial for ensuring they stick properly to products. However, adhesives can deteriorate over time, reducing their effectiveness.
- Chemical Breakdown: Adhesives can break down due to chemical changes over time, especially if exposed to air, moisture, or extreme temperatures.
- Loss of Stickiness: Over time, the adhesive may lose its tackiness, making it difficult for the label to adhere properly to surfaces.
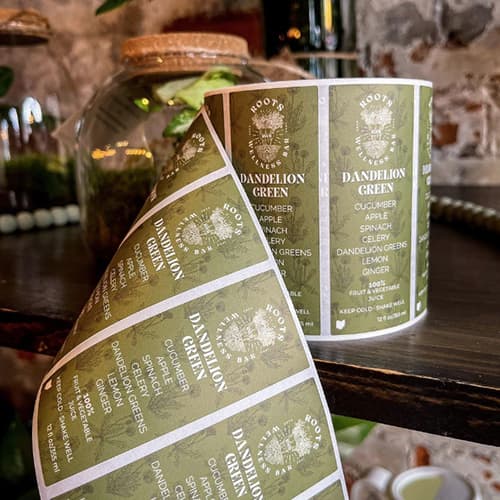
Impact of Storage Conditions (Temperature and Humidity)
The environment in which labels are stored significantly impacts their shelf life.
- Temperature: Ideally, labels should be stored at a stable, moderate temperature. Extreme heat can cause adhesives to melt or become overly sticky, while cold temperatures can make them brittle.
- Humidity: High humidity can cause labels to absorb moisture, leading to adhesive failure and paper degradation. Conversely, very dry conditions can cause labels to become brittle and crack.
Best Practices for Storing Unused Labels
Optimal Storage Conditions
To maximize the shelf life of your labels, it's important to store them under optimal conditions.
- Temperature: Maintain a consistent storage temperature of around 72 degrees Fahrenheit (22 degrees Celsius).
- Humidity: Keep the relative humidity around 50% to prevent labels from becoming too dry or too moist.
Avoiding Environmental Extremes
Protect your labels from environmental extremes that can degrade their quality.
- Avoid Sunlight: Direct sunlight can cause labels to fade and adhesives to break down.
- Protect from Moisture: Store labels in a dry area to prevent moisture absorption and potential mold growth.
Signs That Your Labels Have Expired
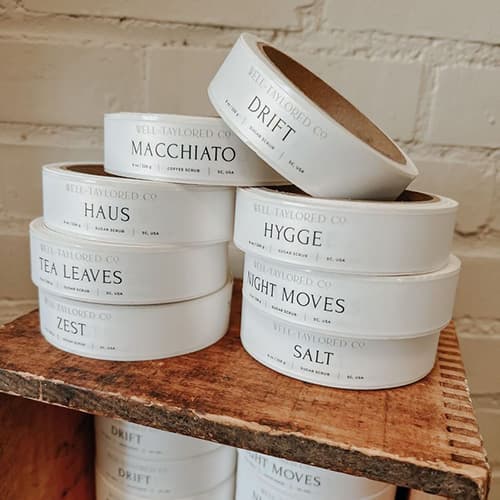
Loss of Adhesive Strength
One of the most common signs that labels have expired is a noticeable decrease in adhesive strength.
- Peeling Labels: If labels are peeling off easily or not sticking well, the adhesive may have deteriorated.
- Slippery Surface: A tacky or slippery feel to the adhesive side can indicate that it has broken down.
Changes in Material Appearance
Physical changes in the label material can also indicate that they are no longer usable.
- Color Fading: Exposure to light or environmental conditions can cause labels to fade, making them look old and unappealing.
- Brittleness or Cracking: Labels that become brittle or crack easily have likely been stored improperly or are past their usable life.
Recommendations for Managing Label Inventory
Ordering the Right Quantities
Managing label inventory efficiently can help prevent waste and ensure you always have fresh labels on hand.
- Demand Forecasting: Use sales data to forecast demand accurately and order labels in appropriate quantities.
- Just-in-Time Ordering: Consider just-in-time (JIT) ordering practices to minimize inventory and reduce the risk of label deterioration.
Regularly Checking Stored Labels
Perform regular checks on your stored labels to ensure they remain in good condition.
- Inventory Rotation: Use a first-in, first-out (FIFO) system to ensure older labels are used before newer ones.
- Periodic Inspections: Regularly inspect labels for signs of deterioration or damage, such as fading, cracking, or loss of adhesive strength.
FAQs
How long can I store unused labels before they expire?
Generally, unused labels can be stored for 9-12 months under optimal conditions. The shelf life can vary based on the material and storage environment.
What are the best conditions for storing labels?
Labels should be stored at a stable temperature of around 72 degrees Fahrenheit (22 degrees Celsius) and a relative humidity of 50%. Avoid direct sunlight and moisture.
Can expired labels be revived or reused?
Typically, expired labels cannot be revived. If they have lost adhesive strength or show signs of deterioration, it’s best to replace them to ensure proper adhesion and appearance.
What are the signs that my labels are no longer usable?
Signs that labels are no longer usable include loss of adhesive strength, peeling, fading, brittleness, and cracking.
How can I prevent label waste and manage inventory effectively?
To prevent label waste, order labels based on accurate demand forecasts, use a FIFO system, and store labels under optimal conditions. Regularly inspect your inventory to identify and use older labels first.
Ready to Order Custom Labels?
Ensuring your labels stick properly is crucial for product presentation and durability. At Wizard Labels, we specialize in high-quality custom labels tailored to your needs.
Visit our custom product labels page to get a custom quote today and learn more about the best materials for your labels.